Линия по проиводству труб Ø60 мм - Продам в Анталии
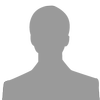
Турция, Анталья, Анталия, Şafak Mh 5018 Sok Sanayi Sitesi 7A Blok No:43 Kepez
Детальное описание
ДИАМЕТР ТРУБЫ: Ø10 - Ø60 mm
ТОЛЩИНА: 1.00 mm - 3.00 mm
МОЩНОСТЬ: 450 kW
ШИРИНА РУЛОНА: 40 - 200 mm
ВНЕШНИЙ ДИАМЕТР РУЛОНА: Ø1000 - Ø1800 mm
ВНУТРЕННИЙ ДИАМЕТР РУЛОНА: Ø480 - Ø520 mm
ВЕС РУЛОНА: МАКС. 3 ТОННЫ
СКОРОСТЬ: 20-120 М/МИНУТА
ПИЛА ЛЕТЯЩАЯ ПИЛА - ГОРЯЧАЯ РЕЗКА
СВАРКА: 200kW solid state HF
ОБЩАЯ ДЛИНА ЛИНИИ: 15М
СЕКЦИИ ЛИНИИ:
*УСТРОЙСТВО РАЗМОТКИ ЛЕНТЫ
*АППАРАТ ДЛЯ СВАРКИ КОНЦА ЛЕНТЫ
*СПИРАЛЬНОЕ НАКОПЛЕНИЕ ГОРИЗОНТАЛЬНОЕ
*ГРУППА ФОРМОВКИ
*СВАРОЧНОЙ ГРУППА
*ОХЛАЖДАЮЩИЙ ТУНЕЛЬ
*КАЛИБРОВОЧНАЯ ГРУППА
*ПИЛА
*УПАКОВОЧНАЯ ГРУППА
*ЭЛЕКТРИЧЕСКАЯ ГРУППА
TECHNICAL PROPOSAL
1 GENERAL DESCRIPTION;
The proposed Tube Mill is a combination of equipment installed in a line for the production of High Frequency Induction Welded (HFIW) carbon steel tubes. The process involved is cold forming of carbon steel strip in circular shape, longitudinal welding,sizing ,converting into specified shape and cutting to pre determined length.
Ø127 high-frequency welded tube mill line is designed to produce round tubes with diameter of Ø60-Ø127mm with Wall thickness of 1.5-4.0mm. This line utilizes roll forming to process steel strip into various shapes. Using high frequency induction heating ,this line is capable of producing section material of various diameters and sizes by squeezing weld seam together into closed shape. The products conform to BS/ASTM standard. Adopting the advantages of the equipment of the same kind at home and abroad, each element of the line is designed with new ideas. The application of advanced technology,PLC automatic control system and British Eurasia Digital speed regulating unit ensure that the production line Works reliably operates and British Eurasia Digital speed regulating unit ensure that the production line Works reliably operetes and maintains easily. Being the best production line in China it can also compete with the advanced ones in the World.
Advantages of the line: It is easy to operate adjust and maintain with good welding seam quality and rigid machine structure.
2 TUBE MILL LINE TECHNICAL SPECIFICATION:
2.1 Direction of Operation: From left to right
2.2 Total Power:800kw
2.3 Compressed Air:5m2/min Pressure :0.4-0.7 MPa
2.4 Capascity of cooling liquid:20t/h-30t/h
2.5 Tube welding speed:10-80m/min
(Square and Rectangular Hollow Shapes are produced at lower speeds depending on side to Wall thickness ratio)
3 RAW MATERIAL SPECIFICATION:
3.1.1 Material: Carbon Steel,Cold or Hot Rolled pre slit strip coils of weld able grade with max. 0.2% carbon
3.1.2 Material: ob≤520 Mpa os≤340 Mpa
3.1.3 Strip thickness: Min 1.5mm Max 4.0mm
3.1.4 Width of strip:200-400mm
3.1.5 Strip Width Tolerance:±0.1mm
3.1.6 O.D of coil:Ø1000-Ø1800mm
3.1.7 I.D of coil:min 480 mm ( to be confirmed by Buyer)
3.1.8 Coil weight:5.0 T( MAX)
4 PRODUCT SPECIFICATIONS:
4.1.1 Round Tube Diameter: Min Ø60mm MaxØ127mm
4.1.2 Round tube Wall thickness : min 1.5mm max4.0mm
4.1.3 Sizing length:4m-8m
4.1.4 Cut Length Tolerance ±3.0mm
4.1.5 Tube Thickness/Diameter Ratio: Min 0.02 Max 0.10
4.1.6 Tube Stndart: Apply to relevant international standard ASTM A513,ASTM A500
4.1.7 Outside Diameter Tolerance ±0.2%or ±0,15
5 DIAGRAM LAYOUT
Coil material-Uncoiling –Shear&Weld-Horizontal spiral accumulator-Forming Welding Cooling – Sizing-Flying saw-Packing machine.
6 MAIN TECHNICAL SPECIFICATION OF EACH EQUIPMENT
6.1 Mechanical double cone uncolier
The uncolier is a key unit in the mill line, ıt s mainly used to support the strip coil and,feed the strip into the next process.
1) Type: double cone
2) Coil weight:5T
3) O.D of coil 1000-1800mm
4) MandrelDiameter:480-520mm
5) Steel trip width:200-400
6.2 SHEAR AND WELDER
Shear and welder mainly Works for cutting clear of both ends of every strip and welding their butts with each other so as to ensure continuous production of pipes.
1)Maximum cutting thickness:4.0mm
2)Maximum cutting width:400mm
3)Mode of welding:manuel
6.3 HORIZONTAL ACCUMULATOR
Working principle:Hydraulic cylinder of strip feding unit holds down steel strip. The feeding motor drives the feeding roll to fill strip into the accumulator by friction force. The main motor rotates supply roll of the accumulator cage to store steel strip in the inner and outer storage zone. The drive motor will stop after one coil finished,and will resume feeding after cutting and welding of another coil.
Fixed rim accumulator:strip lead in from outer rim,and dischrge from center.
6.4 FORMING AND SIZING MILL
Forming Method: w forming,bottom line of tube constant for all sizes.
1)Feeding&Leveling of Roll Forming mill:1 set
1.1 Leveler:1 set
TYPE:5 Roll driven type,two on the upper and 3 on the lower
1.2 Guiding roll:1 set
For assuring the supply strip steel steady
1.3 Horizontal stand of forming:7 sets
Roll shaft diametr:80mm
Portal type stands
Material of horizontal stand:cast steel
Roller exchange:pulled shaft from side
1.4 Vertical roll stand:9 sets
Shaft diameter of vertical stand:cast steel
2)WELDİNG DEVİCE:1 SET
2.1 Weld seam guide-roll table:1 set
Idle 2 roll type,portal type stands,bearing re installed for combination with roll shaft.
The upper fin roll be adjusted by hand screw for up/down direction in order to change the center distance. The two available for lifting, horizontal moving and rotating.
2.2 Squeeze roll:1 set
It is of 4-roll type
2.3 Outside weld scarfing device:1 set
It has 2 sets of cutters whose height can be adjusted by manual. The cutter racket are pneumatic system for quick lifting and retreating of cutter.The height of support rolls can also be slightly adjusted.The cutter head is of hard alloy material , and the cutter rod is low carbon steel.
2.4 Iron roll:1 set
2-roll idle type,adjustment type is same as horizontal roll.
Material of horizontal stand:cast steel
2.5 Cooling device:1 set
It is shower type. It consists of water trough and piping. The water supplying system for cooling water be supplied by the customer s side. The length of the water trough is 3000mm and the water flow be regulted through valves.
3) H.F. WELDER (300KW SOLID STATE): 1 SET
Working principle: An induction coil connected to high frequency power supply encompasses the formed tube profile to induce a high frequency current in the tube profile. With skin effect and proximity effect of high frequency current , induced electricity is concentrated onto bonding surface of the tube profile fringe. The resistance of the metal itself heats up the profile fringe quickly to welding temperature , and finishes pressure welding when tube fringes squeezed together by squeezing roll.
This machine is a PC controled high frequency energy saving type induction-heating device.
Characteristics : Due to application of advanced PC processing technology, this machine is capable of infinite adjustment of output power in a wide range, as well as stabilization of main curent voltage by feedback. Over current is monitored with PC to ensure reliable protection.
4) SIZING MACHINE: 1 SET
4.1 Horizontal stand: sets
For others details please see the forming machine section.
4.2 Vertical stand: 5 sets
For others details please see the forming machine section.
4.3 Rough straightening machine: 3 sets
Each set is consists of 4 pieces roll and each roll be adjusted by ball screw. The cross roll stand be wholly lift and horizontal moving or retuning.
4.4 Driving Device: 1 set
4.5 Driving Motor: DC motor 160 KW 1 set
6.5 DC MOTOR FEEDER / DRIVE (1 DC MOTOR)
6.6 FLAYING SAW:
1)Type : Hot saw, friction saw
2) This machine comprises base , rack and pinion , saw car , tube clamping tools, speed testing system , lift roller stand.
3) Determine the cutting position and respond quickly to synchronize the cutting equipment with line speed.
4) Keep cutting equipment in pace with line speed , cutting mecjanism react to cut off the tube.
5) Flying saw functions to cut welded tube into fixed lenght in line. It utilizes high speed rotary shear , and depending on computer and combination of rack-and-pinion to perform tracking cutting.
6) Main technical indexes:
Carriage moving motor: 30 KW
Cutting motor: 30 KW
Car driving: be driven by motor and reduction gear
Tube clamping tools: guide cusion
Cutting length: 4 – 8 mm
Precision of cutting: ±3.0 mm
6.7 Rolls and Spacers and Roll Templates
1) Rolls
Rolls are manufactured out of AISI D3 or E52100 (JIS SKD1 or SUJ2). Material is annealed, hardened and tempered to get hardness of 60+2 HRc. Rolls profiles are precisely turned at high speed on CNC Turning machine using ceramic tips to get the desired surface finish.
2) Spacers
Roll Spacers are made of alloy steel, hardened & tempered and machine finished all over. Faces are ground to maintain the centerlineof Tube Mill.
3) Roll Templates
Roll Templates are used for checking the profiles of rollers each time they are profiled. Templates are manufactured of carbon steel and EDM wire cut.
6.8 Driven Roller Run out Table
The run out table takes the cut tubs from the cut off section out of the line. The run out table will be driven type. Arrangement is provided for taking the tubes out of run out table on both sides so that in one side good tubes are taken out and on other side bad tubes are taken out. Fixed type run out table is provided as the forming is based on bottom line.
Type | Driven Rollers Type |
Total Length | 18 Meters |
Tube Dumping | Both side through star Wheel by AC geared brake motor |
Tube Inspection Table | Fabricated Steel Structure |
Tube Collectors | Fabricated Steel Structure |
Создано 22.03.2019 Изменено 22.03.2019